Rohrdorfer starts ethylene production from carbon dioxide
Rohrdorf, July 24, 2024 – Rohrdorfer has successfully started ethylene production from carbon dioxide (CO2). In a newly developed process, CO2 generated during cement production is recovered and converted into ethylene. Following a test phase, production is to be scaled up to an industrial scale, thereby establishing a seamless CO2 circular economy. The long-term goals are independence from fossil raw materials through regional value creation and climate-neutral cement production.
Ethylene is a sought-after and extremely versatile product. It is the starting material for many substances such as polymers, kerosene, resins, silicones and textiles. Rohrdorfer uses the CO2 produced during cement production and converts it into ethylene. The technology is based on a new type of CO2 electrolysis that can be used to produce both formic acid and hydrocarbons such as ethylene. With the “CO2 to ethylene” approach, it is possible to establish a seamless circular economy and become independent of fossil raw materials.
Innovative project for CO2 electrolysis
“CO2 to ethylene” is part of the H2-Reallabor Burghausen – ChemDelta Bavaria research project. 37 partners from industry, SMEs, start-ups and research are working towards the goal of using hydrogen as a material basis in the chemical industry. The project was officially launched in April 2023, with the Rohrdorf Net Zero Emission team investing several months in research and development based on the findings from the previous “CO2 to formic acid” project. As a result, the team was able to adapt the plant for the production of green ethylene. In the first step, a test stand for a few 100 grams of ethylene per hour was put into operation. This will soon be followed by an industrial-scale demonstrator with a conversion rate of up to six kilograms per day. The next scaling step is planned for 2026 and will convert 1 kilogram of CO2 per hour into ethylene on a container scale.
Rohrdorfer ethylene can be easily processed further
A new feature of the system is its advantageous operation at a pressure of 30 bar. At these pressure ratios, the product mixture can be easily filled into pressurized gas cylinders through a sampling point. At this pressure ratio, transportation to the partners of the H2-Reallabor Burghausen is no problem. Customers from the chemical triangle can easily test and further process the ethylene. “The special combination of pressure, scale of production and self-developed technology make our process unique,” says Dr. Alexander Beck, employee at Carbon Capture and Utilization in the Net Zero Emission team in Rohrdorf. “The fact that we are integrated into the H2 real laboratory opens up many opportunities for the regional value creation of our carbon dioxide.”
The Rohrdorf research project “CO2 to ethylene” is 50% funded by the German Federal Ministry of Education and Research and will run for four years. The funding amounts to 1.67 million euros.
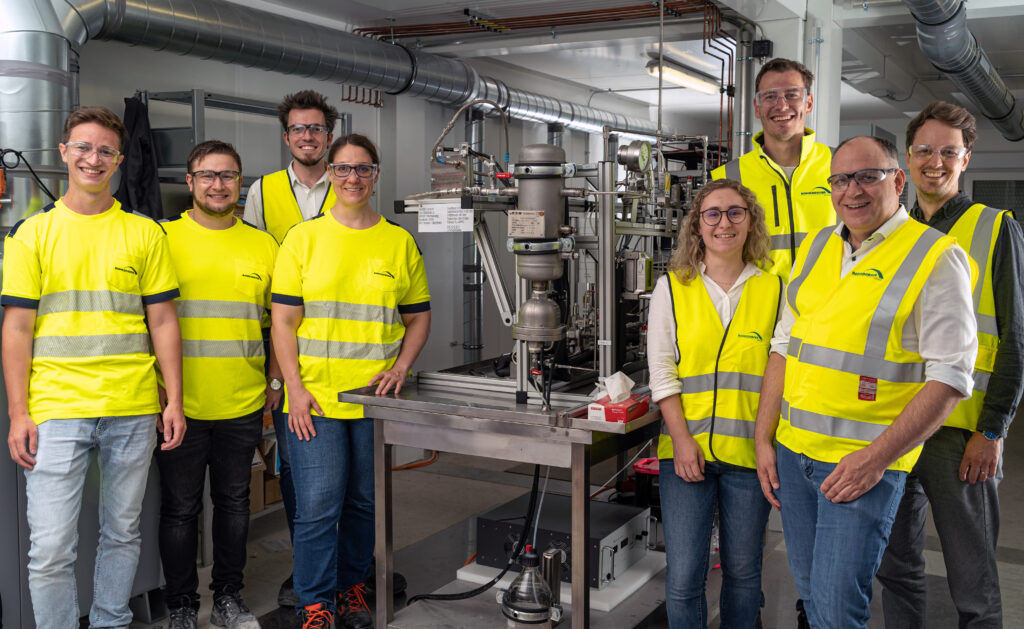
From left to right: Alexander Lechner, Raphael Gratzl, Dr. Alexander Beck, Dr. Katharina Mairhofer, Pia Hillinger, Thomas Mairegger, Dr. Philipp Stadler, Dr. Ralph Freund.