Pilot Plant Direct CO2 Electrolysis to Formic Acid
FIRST CEMENT PLANT IN GERMANY TO BUILD A CO2 CAPTURE PLANT
Germany’s first plant for carbon capture and utilization (CCU) of in the cement industry sequesters up to two tons of carbon dioxide per day. Rohrdorfer targets a net-zero cement manufacture by 2038. Named “Aurora 1” the CCU-plant is continuously operated by engineers from Rohrdorfer’s Net Zero Emission Labs, a spin-off from Rohrdorfer, using directly flue gas from the rotary kiln of the cement manufacture process..
CO2 from cement production is thereby captured using an amine scrubber and fed into a desorber, where it exits as purified CO2 at 99.95%.
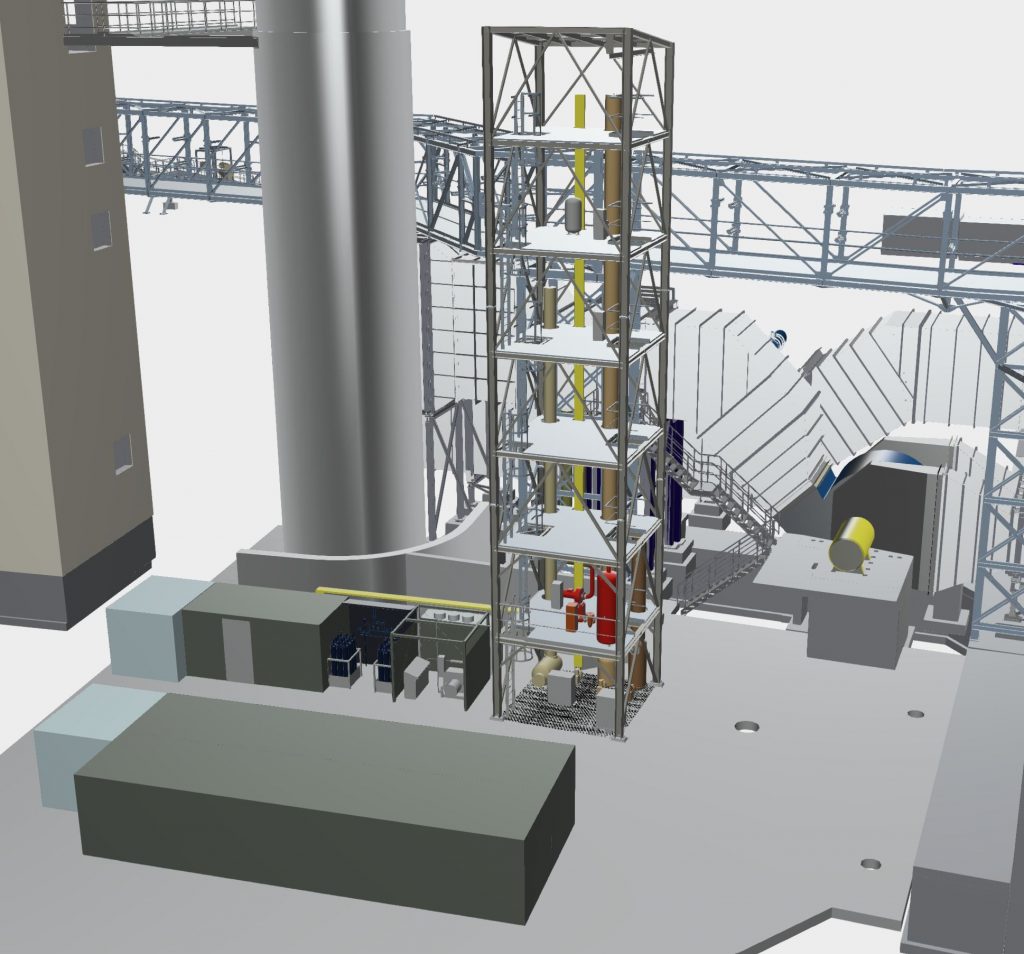
Amine-based capture technology is state-of-the-art in various industry branches, among them coal-fired power plants, but also chemical gas refining, waste incineration and biogas treatment. However, the technology possesses a lower technology readiness level when it comes to its application in cement industry.
Flue gas from cement productions have high O2 concentrations and aggressive trace gas components that affect the amine treatment detrimentally. The cement manufacture operates dynamically and different modes, such that fluctuations vary the flue gas stream and composition.. Therefore, Rohrdorfer installed the amine pilot thus to investigate the technologies´ applicability in a real-life i.e. cement production environment..
The yearlong operation of Aurora-1, commissioned in 2022, has led to valuable insights about the effectiveness of the separation technology in an industrial application. With a designed daily capture capacity of 2 tons, the engineers at Rohrdorfer identify the optimal amine solution and process conditions for treating the cement kiln gas. Likewise, the team is close to find the sweet spot for the optimum capture condition so that energy consumption, amine degradation and corrsosion are minimized. One future perspective are new-innovative generation-3 amine solvents, that can further work on an optimium energy efficiency paired with unique real-life studies on long term effects, optimized process windows and the operational strategies to scal e the plant. In addition, the NZE-team monitors the long-term operation campaigns to derive a conceptual engineering and process design in order to estimate the feasibility of the amine scrubbing technology at full industrial level.
The recovered CO2 maybe stored (Carbon Capture and Storage, CCS) and reused (Carbon Capture and Usage, CCU), respectively. Rohrdorfer is currently exploring CCU e.g. using CO2 as carbonic acid for food additives, sparkling water and for beer, as well as greenhouse fertilization of tomatoes, garlic, and as technical gas for pressurized fire extinguishers, as refrigerant in heat pumps, and as neutralization agent for geothermal energy projects.
A central CCU route is the conversion of CO2 into formic acid by renewable electricity and water. Rohrdorfer implemented its proprietary CO2-to-formic demonstration plant at 1kg/h capacity. The technology is currently prepared for industrial applications by licensing and partnerships towards large-scale production for biochemical, food, agricultural and related chemical applications.
By this real-life demonstrators Rohrdorfer paves the way towards industrial decarbonization thereby creating regional value in Austria, Italy and Bavaria (sourth Germany) as technology and innovation lead.
For Rohrdorfer, the demonstration plants for CCU and CCS are integral to decarbonize its cement manufacture process. The the recovery of CO2 , particular of the hard-to-abate emissions, is vital to strengthen Rohrdorfer´s economic viability thus to implement a net-zere cement production lastest by 2038. These CCU plants are pivotal for the regional environmental protection and resource conservation in line with Rohrdorfer´sESG (Environmental, Social, Governance) strategy.
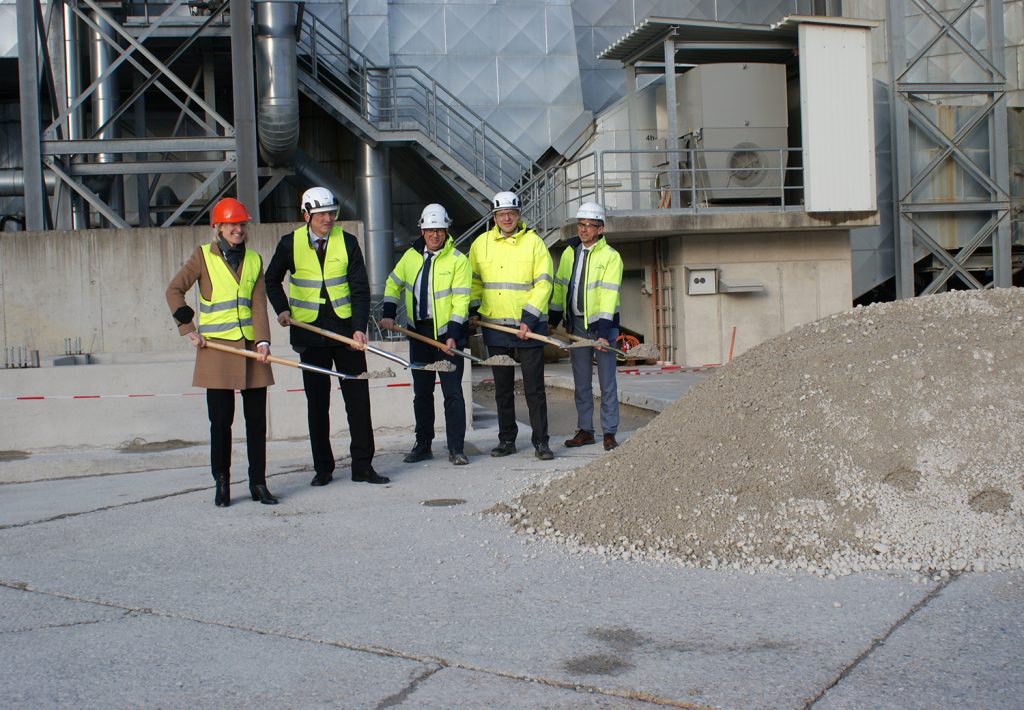